Are unexpected valve failures disrupting your plant’s operations or risking safety? Plug valves are integral to many industrial systems. When chosen and maintained correctly, they provide efficient flow control with minimal resistance.
From processing plants to water systems, these valves are expected to perform flawlessly. However, problems can arise unexpectedly. A failed plug valve can pause operations or cause severe damage if unaddressed.
The risk extends beyond the valve itself. It can affect entire system sections, leading to higher repair costs and creating difficult-to-resolve safety issues. We know that catching problems early makes all the difference.
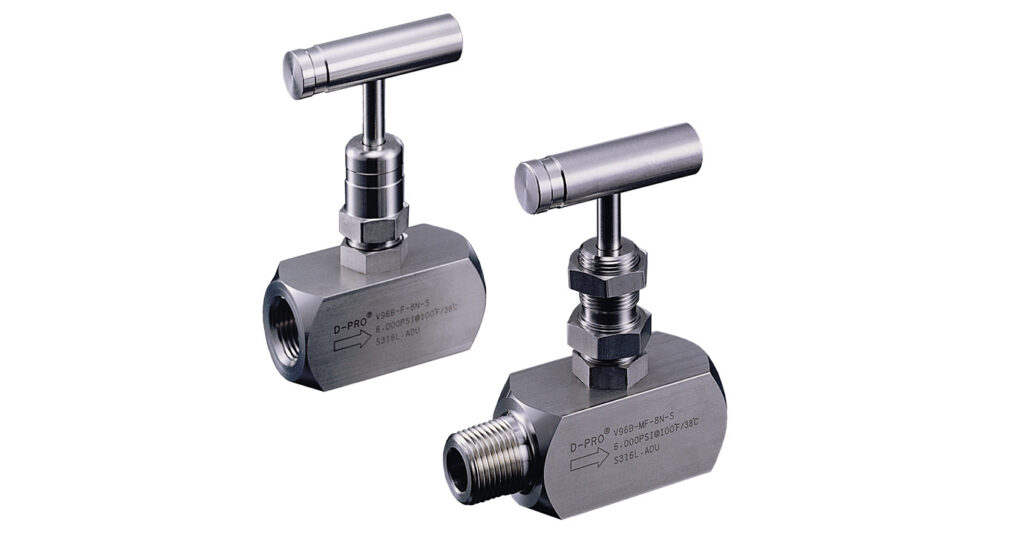
Common Causes of Plug Valve Failures: Understanding the Stressors
What are the root causes of plug valve failures in demanding environments? Plug valves endure significant daily stress, especially with frequent use or under high pressure. Understanding these common causes helps in proactive prevention.
Here are frequent reasons why plug valves fail:
- Wear from Daily Use: Over time, the interior components of a plug valve can wear down. The plug may become harder to rotate or may no longer seal effectively. A weakened seal opens the door for leaks and pressure loss.
- Improper Installation or Misaligned Fittings: If a plug valve is not properly aligned, or if fittings are incorrectly tightened, it creates uneven stress on the valve body. This accelerates wear on internal parts. The valve may then begin leaking far earlier than anticipated. We emphasize correct installation practices to mitigate this risk.
- Exposure to Tough Environments: Malaysia’s warm and humid climate significantly impacts materials. If a valve lacks proper protection from rain, dust, or high humidity, corrosion can develop externally or internally. Once rust sets in, smooth valve operation becomes challenging.
We’ve observed situations like a small packaging facility facing multiple disruptions due to one faulty valve. A new plug valve, installed at a slight angle, initially performed well. However, within two months, it became difficult to turn, affecting pressure flow and halting the entire system. Timely inspection of installation could have prevented this costly downtime.
Early Warning Signs of Plug Valve Issues: Detecting Problems Proactively
How can you identify plug valve issues before they escalate into major failures? Plug valve problems often begin with subtle changes, easy to overlook. Catching these early signs can prevent a larger failure entirely.
Here is what to look out for:
- Stiff or Hard-to-Turn Valve Handle: If rotating the handle requires more force than usual, it may indicate internal friction or early debris buildup. This is often the first sign of an issue within the valve chamber.
- Strange Noises or Shaking: A properly functioning plug valve should operate quietly. Humming, clicking, or vibration during operation suggests parts might be loose or working unevenly. These sounds are critical indicators.
- Signs of Corrosion: Corrosion or discoloration on the valve body or handle, even minor, can weaken outer parts and suggest internal damage. In wet or humid areas like Malaysia, this requires frequent checking.
- Irregular Flow or Loss of Pressure: If fluid flow suddenly slows or becomes erratic, it could mean the plug is no longer sealing correctly. Pressure problems may also manifest as pump strain or increased energy use elsewhere in the system.
Spotting these warning signs early can mean the difference between a quick fix and a long delay. We recommend routinely checking valve handles during inspections. Feel for unusual heat, resistance, or any abnormal movement. Simple checks often reveal clues long before major system failures occur.
Regular Maintenance Practices: Ensuring Long-Term Reliability
Are your plug valves receiving the consistent attention they need for sustained reliability? Plug valves are not “install-and-forget” components. A robust maintenance schedule is critical for catching small issues before they become major problems.
Begin with routine checks. These do not require extensive time but should be frequent, especially in production-heavy setups. Look for buildup, corrosion, or signs of excess pressure. Do not wait for the valve to feel “off.”
Regular cleaning is also vital. Debris and residue can settle around the seal, creating uneven pressure points internally. Basic cleaning with appropriate tools helps prevent gunk accumulation. If the valve is exposed to water, steam, or chemicals, increase cleaning frequency. Always dry components thoroughly before reassembly.
Proper lubrication is crucial for smooth movement. Some plug valves require specific lubricants. It’s essential to select a lubricant compatible with the valve’s material, whether lined or stainless steel. Avoid over-lubrication, which can attract dirt and cause excess wear.
Do not overlook adjacent fittings. Loose or mismatched pipe fittings can add strain to the plug valve. During valve checks, ensure all surrounding fittings are secure, correctly aligned, and free from thread damage or rust.
Adhere to this comprehensive inspection list: Check for leaks, wear, or visible corrosion. Rotate each valve handle to test firmness. Examine adjoining pipe fittings for signs of leakage or misalignment. Apply the correct lubricant and remove past residue. Replace any parts showing obvious signs of stress, aging, or metal fatigue.
When to Consult a Professional: Strategic Expert Intervention
Are your quick fixes temporary, or is your system expanding beyond your current maintenance capabilities? There comes a point where routine maintenance is insufficient. If problems persist or return swiftly after basic repairs, professional expertise may be necessary.
Repeat failures are a strong indicator. If the same valve consistently jams, leaks, or causes pressure dips, the root issue might be unresolved. A professional can precisely track the problem to its source, potentially involving pressure line testing or vibration analysis across the pipe network.
Professional help is also essential when your system expands or changes. As more sections are added or higher demands are placed on pipelines, previously adequate plug valves may no longer be suitable. An expert can assess your current design against new loads, recommending optimal solutions.
Some valves require specialized tools for disassembly and testing. This is particularly true for high-pressure applications. Attempting these tasks without the correct equipment risks internal valve damage, which can cause leaks and shorten valve life.
A professional offers not just skill, but deeper insight into system-wide problems. Their specialized test tools and extensive experience often detect issues unidentifiable through standard checks. Especially in Malaysia’s climate, superficial damage can hide severe internal issues.
Therefore, if your maintenance team faces recurring valve issues, you plan a system upgrade, or flow control becomes erratic, consult a trusted technician. A second set of expert eyes can prevent minor issues from escalating into widespread, costly disruptions.
Keeping Your Plug Valves Reliable: Simlecco’s Commitment
Plug valve failure is rarely random. It often stems from everyday practices. Knowing the necessary checks, identifying crucial warning signs, and understanding when to seek professional help are all vital for system stability.
We advise never ignoring minor issues. A tiny leak, slight rusting, or a stiff handle may seem insignificant. However, they are often the first indications of deeper problems. Like all moving parts, valves require regular care. For exposed or frequently used valves, more frequent inspections are necessary.
Ensure correct installation, use the best available fittings, and guarantee strong sealing from the start. In Malaysia’s high humidity and regular rain, plug valves can wear faster than expected. Consistent checks, ongoing care, and timely replacement of faulty parts minimize downtime and ensure safe system performance.
Even if valves are out of sight, their failure impacts the entire system. Proactive maintenance ensures fewer surprises and smoother operations. For reliable performance built for industrial demands in Malaysia, choose the right plug valve from Simlec Co. Our dependable materials and expert design support long-term system performance.